Our Plants
Mie Plant
A large-scale production center
for semiconductor process gases and
specialty gases that open the way to the next generation
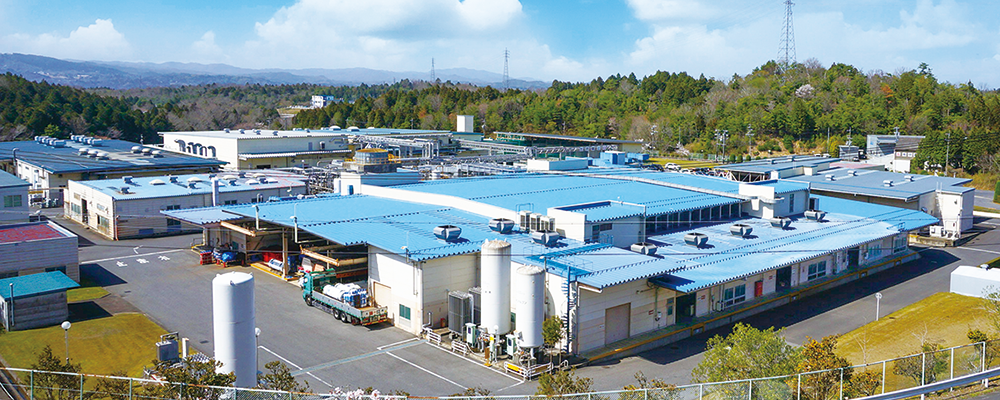
Characteristics
The Mie Plant is the largest of the company’s four plants, and specializes in the production of semiconductor process gases and high-purity gases.
Semiconductor process gases are produced in dedicated buildings which operate as a single large center for the prompt supply of high-quality gases to semiconductor manufacturers in Japan and overseas. The main buildings include the chemical synthesis production building, monosilane building, MO building, and cylinder maintenance building.
High-purity gases are produced by pursuing thorough measures to ensure high purity, such as by attaching refining equipment to all gas types.
Main products handled
- High-purity gases (carrier gases, gases for atmosphere control, etc.)
- Semiconductor process gases (for doping, epitaxial processes, cleaning, etching, etc.)
- Process gases for compound semiconductors (AsH3,PH3,B2H6, etc.)
- Gases for photovoltaic generation (H2Se, etc.)
TOPIC
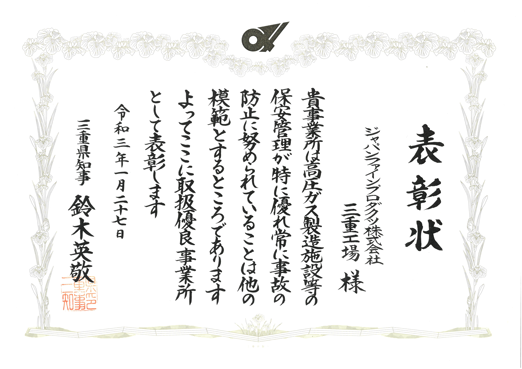
Mie Prefecture Governor’s Award
The Mie Plant was awarded the Mie Prefecture Governor’s Award in January 2021 in recognition of its long years of meritorious work in Mie.Main Building
A sophisticated specialty gas plant designed to be a step ahead of the times
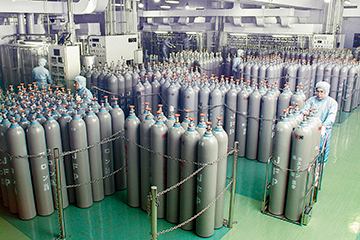
Cylinder management
Large-volume liquefied gas containers
A variety of large containers enables supplies of large volumes of gases. They are polished to an inside surface roughness of Rmax˂1µm. We also have large tanks (such as for ammonia) to meet large-volume needs of mass production plants for 300mm wafers.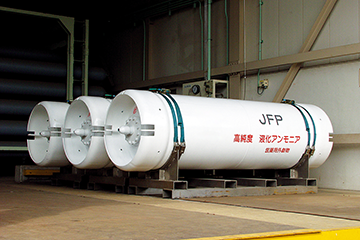
Air shower for incoming cylinders
Operations involving semiconductor process gases are performed in a clean room.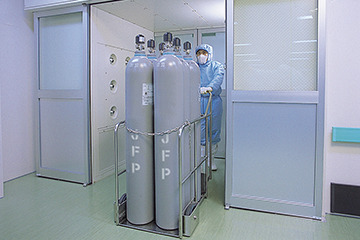
Filling
Particle purging system
Clean specification products are thoroughly purged of particles using particle-free nitrogen gas.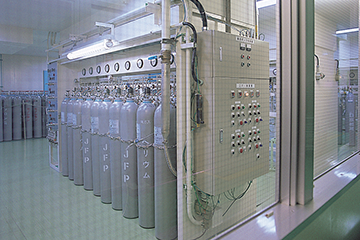
Clean room filling equipment
High-precision gas measuring is performed in a clean booth using a precision load cell, and clean gas purged of particles using a high-pressure filter, is filled in cylinders. Furthermore, a statistical process control (SPC) system is used to enhance mixing precision.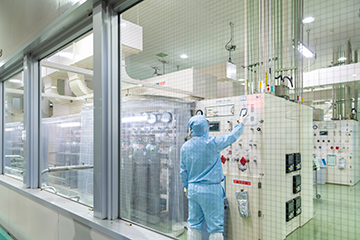
Cylinder carriers
The introduction of cylinder carriers has enabled efficient transport of cylinders within the production process.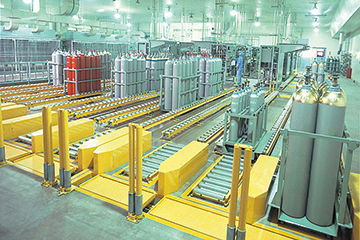
Analysis & inspection
Analysis room
Analyzers calibrated and controlled using our high-precision standard gases ensure high-accuracy, high-sensitivity analyses.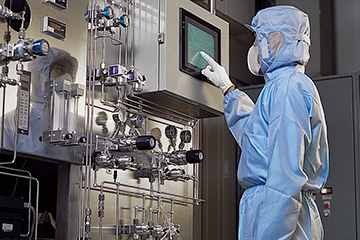
Storage & management
Abnormality monitoring system
The entire plant is constantly monitored for gas leaks and other abnormalities.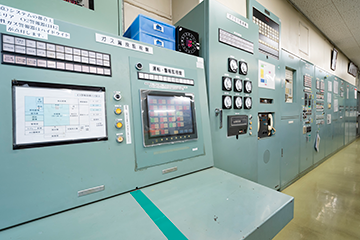
Cylinder storehouse
This is the largest storehouse for specialty gases in Japan. By possessing an abundant stockpile base halfway between the Oyama Plant (Tochigi Prefecture) and Kitakyushu Plant, the Mie Plant plays an important role in terms of logistics.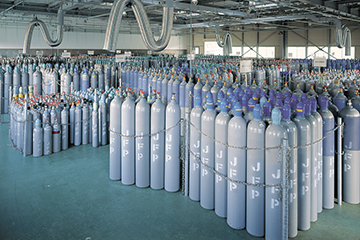
Chemical Synthesis Production Building
A large-scale facility dedicated to the production of hydrogen selenide
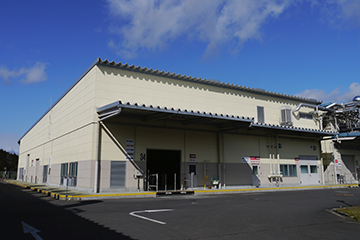
Monosilane Building
A facility dedicated to the production of monosilane
This building is dedicated to the production of monosilane (SiH4), a process gas for semiconductors. In response to increasing demand, it is capable of receiving large volumes of raw materials and filling large volumes of the gas while realizing reduced manpower and rationalizing logistics operations.
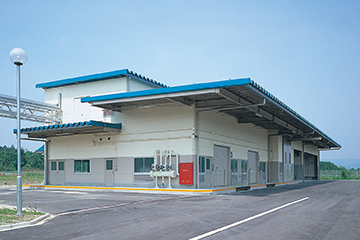
Receiving raw materials
Trailers
Raw materials are received in large volumes using trailers dedicated to carrying curdles (bundles of cylinders).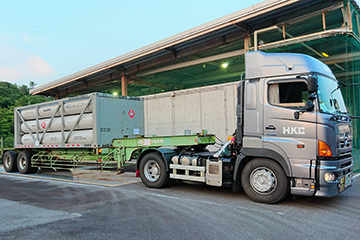
Filling
Compressor yard
A diaphragm-type compressor with no sliding parts is used.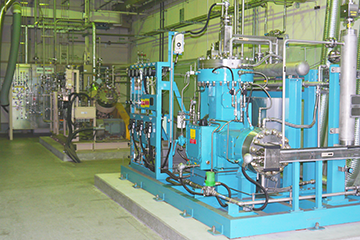
Monosilane filling equipment
The ISO module on the transport vehicle can be connected directly to the filling equipment panel. After attaching the cylinder, it is filled, while paying full attention to safety.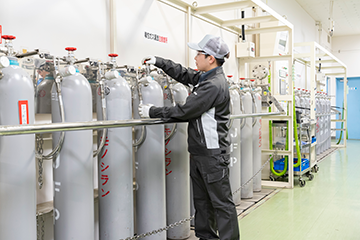
Analysis & inspection
Analysis & inspection room
All processes, from the acceptance inspection of raw materials to final product inspection, are tracked in real time. All facilities are constantly monitored by a thorough security system.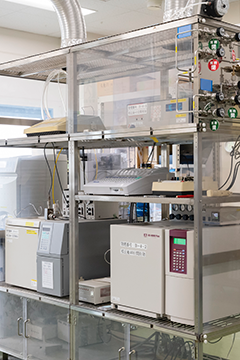
Central management of analyzers
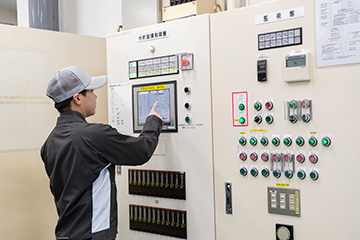
MO Building
Facility dedicated to the production of MO gas for compound semiconductors
MO gases (arsine, phosphine) for metal organic chemical vapor deposition (MOCVD) are indispensable to the manufacture of elements such as for high-speed devices, mobile phones, red laser light, and laser power converters. The MO Building at the Mie Plant boasts one of the world’s largest production of MO gases and refining capacity.
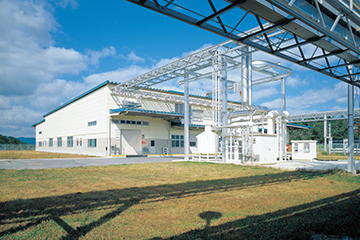
MO gas refining
MO gas refining room
A world-class MO gas refining facility that is capable of removing impurities down to the ppb level, has been constructed.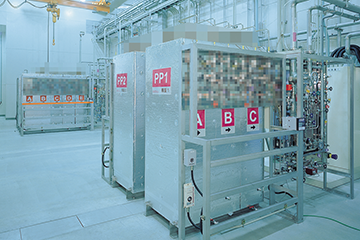
Filling
Filling room
High-purity gases that have been refined to the greatest extent possible are filled in cylinders in a clean room. To respond to mass production needs, five cylinders can be filled simultaneously at a stable quality.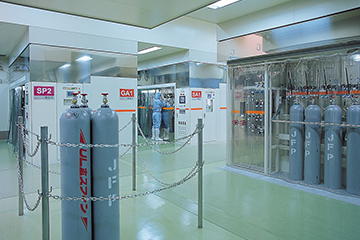
Analysis & control room
The analysis & control room is situated adjacent to the filling room and cylinder storage room. It utilizes advanced instruments such as a gas chromatography mass spectrometer and vacuum FTIR, to realize prompt analysis and control through a framework that integrates production processes. Every effort is made to always ensure the highest quality in line with rigid internal quality standards.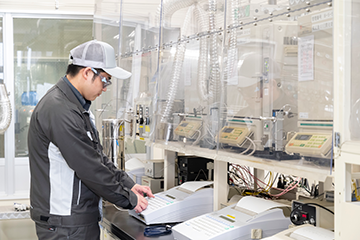
Cylinder Maintenance Building
A facility that realizes shorter production lead times and stable supply through the proper maintenance of cylinders
The supply of high-quality gases in high-pressure cylinders is premised not only the purity of gases, but also on the cleanliness of the inside of cylinders. At the Mie Plant, a dedicated facility and system is in place to perform pressure tests, and to wash and remove impurities from inside the cylinders to the greatest extent possible. Maintaining cylinders in this way directly at the plant helps shorten production lead times and realize prompt response and stable supply.
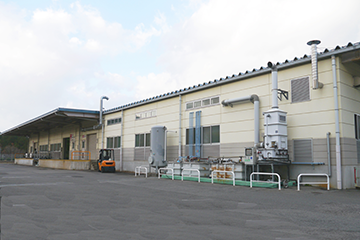
Inside surface shotblasting
Inside surface shotblasting equipment
A high direct-pressure blasting equipment that uses a special grid has been constructed as a method of cleaning the inside of cylinders. Cleanliness is enhanced to the greatest extent possible by using ultra high-purity, high-pressure nitrogen.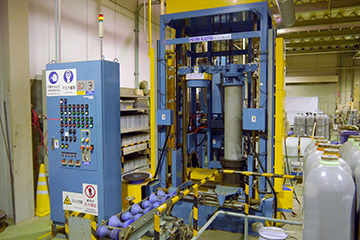
Pressure resistance testing
Pressure resistance testing facility
Statutory pressure testing is performed safely and efficiently in an automated facility. Pressure resistance data is automatically linked to a production information system to ensure safe cylinders.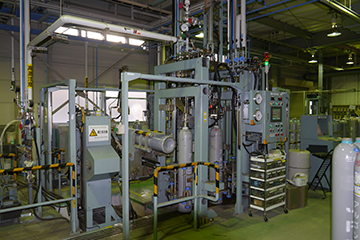
Special washing of cylinders
Special cylinder washing device
The company’s original precision polishing facility for the inside of cylinders has been combined with polishing expertise it has cultivated over more than 30 years, to minimize the inside surface roughness of clean cylinders.The inside of cylinders is automatically washed in a clean environment.
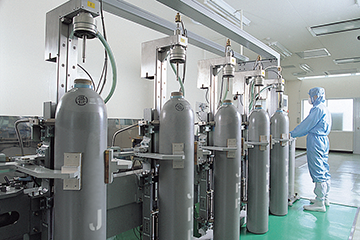
Evacuating the cylinders by heating
Evacuation furnace
After washing the clean cylinders (inside surface roughness Rmax<1µm), they are evacuated in a state-of-the-art evacuation furnace to remove any residual moisture on the inside surface to the ppb level.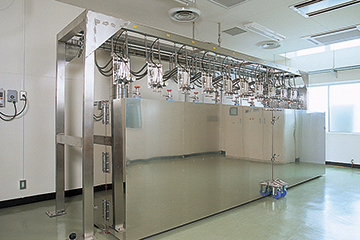
Painting the cylinders
Cylinder painting equipment
The final process involves painting the cylinders using the latest VOC-free paint, which significantly reduces environmental burden compared to conventional organic solvent paints.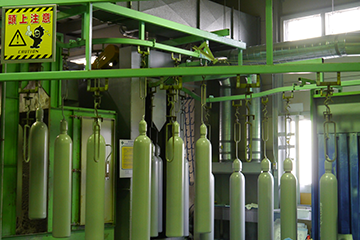